ECO-FRIENDLY: The use of chlorofluorocarbon and hydrochlorofluorocarbon refrigerants in traditional cooling systems and in automobile air conditioning has been widespread for many decades. As part of the Montreal Protocol, a major commercial refrigerant, Chloro-fluorocarbons (CFCs), will be phased out soon because they contributed to the greenhouse effect and the loss of the ozone layer. The compressor in an automobile’s air conditioning system consumes about 10% of the energy available at the crankshaft while running on gasoline or diesel. Because most gasoline and diesel-powered vehicles’ thermal efficiency ranges from 20 to 30 percent in excellent condition, this loss is enormous. The simple line is that air conditioning uses a lot of petroleum.
Because of the continuously changing weather and atmospheric effects, auto air conditioning has become a requirement. As a result of rising gasoline prices, component costs, and vehicle maintenance costs, people are finding it increasingly difficult to afford a car. Several innovative manufacturing improvement theories have been created and implemented in recent years in a variety of industries. An investigation has been made to see if waste heat can be recovered and used to cool a vehicle’s air conditioning system without increasing the cost, weight, or number of components, and making the vehicle more luxury.
Automobile air conditioning is the process of cooling and cleaning the air, as well as lowering the humidity level, and circulating the air. Controls are also in place to regulate the amount and quality of air. These are all things that an air conditioner should be able to do in a perfect world. Ideally, the interior of a vehicle should be kept at a temperature of 20°C to 22°C.
The “comfort range” of climatic load is the equivalent of this. When a car is driven in 40°C sunshine, the interior temperature rises by more than 15°C, and it may even approach 60°C to 70°C due to the addition of heat from the ambient air, sunlight, the engine, the road, and the exhaust system. Compared to alternative heating techniques, heat pumps reduce energy usage, improve heating performance, and reduce environmental impact.
The exhaust heat from a vehicle can be used to power the Vapour compression Refrigeration System (VCRS), minimising the amount of work the engine has to do to drive the compressor. Mechanical vapour compression Cycle is used in the refrigeration process to cool products for both household and commercial applications. Vapour compression refrigeration is used in the majority of residential refrigerators nowadays. The compressor, evaporator, throttling device, and condenser are all part of the vapour compression refrigeration system, which has four major components in total.
Automobiles’ air conditioning systems use a vapour compression refrigeration system, which uses adiabatic work relations for open systems W = – V. dP to manage the refrigerant under adiabatic conditions (where V is volume in m3, dP pressure rise, W is work required to attain dP) If the fluid pressure rises, vapour will absorb more work than liquid since its volume V is so much greater.
As a result, the ideal alternative is a vapour absorption system, which works with liquid rather than vapour, but it requires a high-temperature heat source for separation at high pressure; fortunately, high-temperature exhaust gas is readily available and can meet this need without costing anything. To save energy, this acts as a waste heat recovery system.
Refrigeration system components for vapour absorption. The Vapour Absorption Refrigeration System uses only two components. Those are.
- Refrigerant
- Absorbent
a. Refrigerant
Substances or mixtures used in a heat pump and refrigeration cycle are known as refrigerants. Most of the time, it moves back and forth between the liquid and gas phases. Many different types of working fluids have been employed in the past for this purpose. All of the vapour compression refrigeration system’s processes, such as compression, condensation, expansion, and evaporation, are included in the vapour absorption refrigeration system. Ammonia, water, or lithium bromide are common refrigerants in vapour absorption systems. The condenser and evaporator are where the refrigerant is condensed and then evaporated. In the evaporator, the refrigerant generates a cooling effect, and in the condenser, the heat is released to the atmosphere.
An absorber is a substance that has the ability to take in and hold onto a substance. This technique relies on water as an absorbent. When heated, the ammonia is absorbed by the cold water and released.
Drawbacks of vapour compression refrigeration system:
This approach, despite being the most efficient, nonetheless has a few disadvantages:
- More wear and noise is generated by the compressor in a vapour compression system.
- The amount of effort it takes to compress the gas in the compressor is enormous.
- It can only be used in places where electricity or mechanical power is readily available.
- When the evaporator pressure is reduced, the vapour compression system’s capacity rapidly decreases in eco-friendly.
- At low loads, a vapour compression system’s performance is sluggish eco-friendly.
- The vapour refrigerant exiting the evaporator in a vapour compression system must be superheated so that no liquid may enter the compressor is eco-friendly.
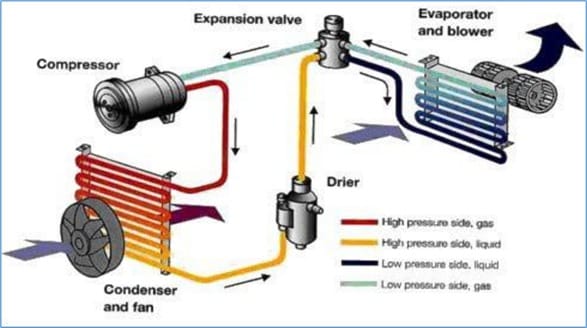
Advantages of using vapour absorption system in automobiles ECO FRIENDLY
When used in road transport trucks, the Vapour Absorption Refrigeration System offers the following benefits:
- The refrigerating unit does not require a separate IC engine for operation in eco-friendly.
- No refrigeration compressor is necessary.
- The refrigerating unit requires no additional effort to operate.
- Reduction in the cost of capital for eco-friendly.
- Fuel costs will be reduced.
- Reduced pollution in the atmosphere.
- Maintenance is reduced in eco-friendly.
- Noise pollution has been reduced in this area of eco-friendly.
ECO FRIENDLY: Compressor, Condenser, Expansion valve, and Evaporator are the four essential components of the vapour compression cycle.
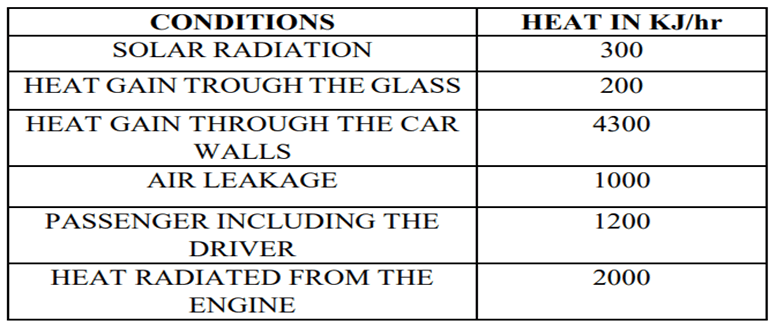
In the table above, we can see the various conditions and how much heat they generate over the course of a day.
The ammonia-water VAR system’s temperature measurements at several points. It is necessary to keep track of not only the temperature of the air conditioning system itself, but also of the various components that make up the system’s cooling system. eco-friendly indicate the temperatures that were measured and recorded with a digital thermometer.
Temperatures noted at various time intervals IN ECO FRIENDLY
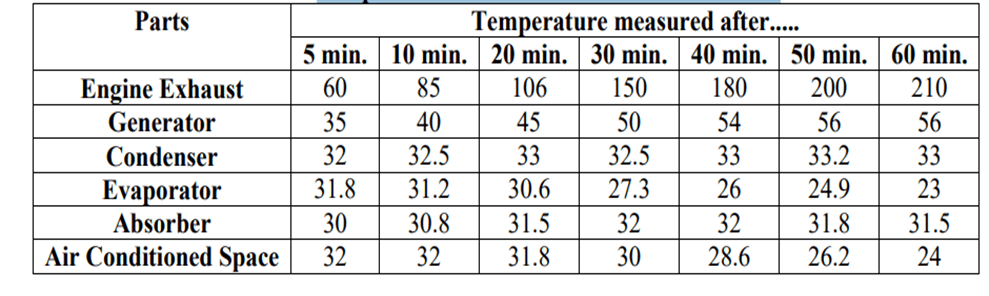
ECO FRIENDLY: The temperature of the area to be cooled begins at 320C Fahrenheit. An increase in exhaust temperature can be seen while the engine runs constantly. Heat transfer media affects the pace at which refrigerator temperature falls as a function of exhaust temperature rise. [25]
Shows the variance in exhaust gas temperature as a function of engine RPM at various loads. When the engine speed is increased, eco-friendly the exhaust temperature rises, and thus raises the temperature to a point where it may drive air conditioning.
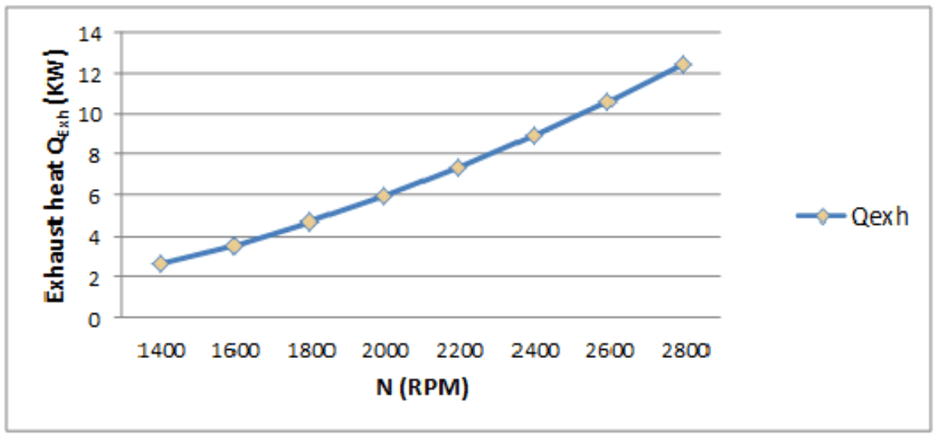
As the engine speed increases, so does the amount of exhaust gas that can be used to evaporate the aqua ammonia solution in eco-friendly.
Vapor Absorption Refrigeration System can be used to design an air conditioning unit for an automobile that uses waste heat from the engine. This system eco-friendly is also environmentally beneficial, as it uses Ammonia (a natural gas) as a refrigerant and does not contribute to the Green House Effect or the depletion of the OZONE layer. Thus, it can be concluded from this that about 35%-40% of heat supplied to the engine in the form of fuel combustion results in eco-friendly useful mechanical work, while the remaining heat is expelled from the system, increasing the amount of entropy; thus, it is necessary to convert this waste heat into useful work.